Understanding inventory and supply chain management
8th July, 2024
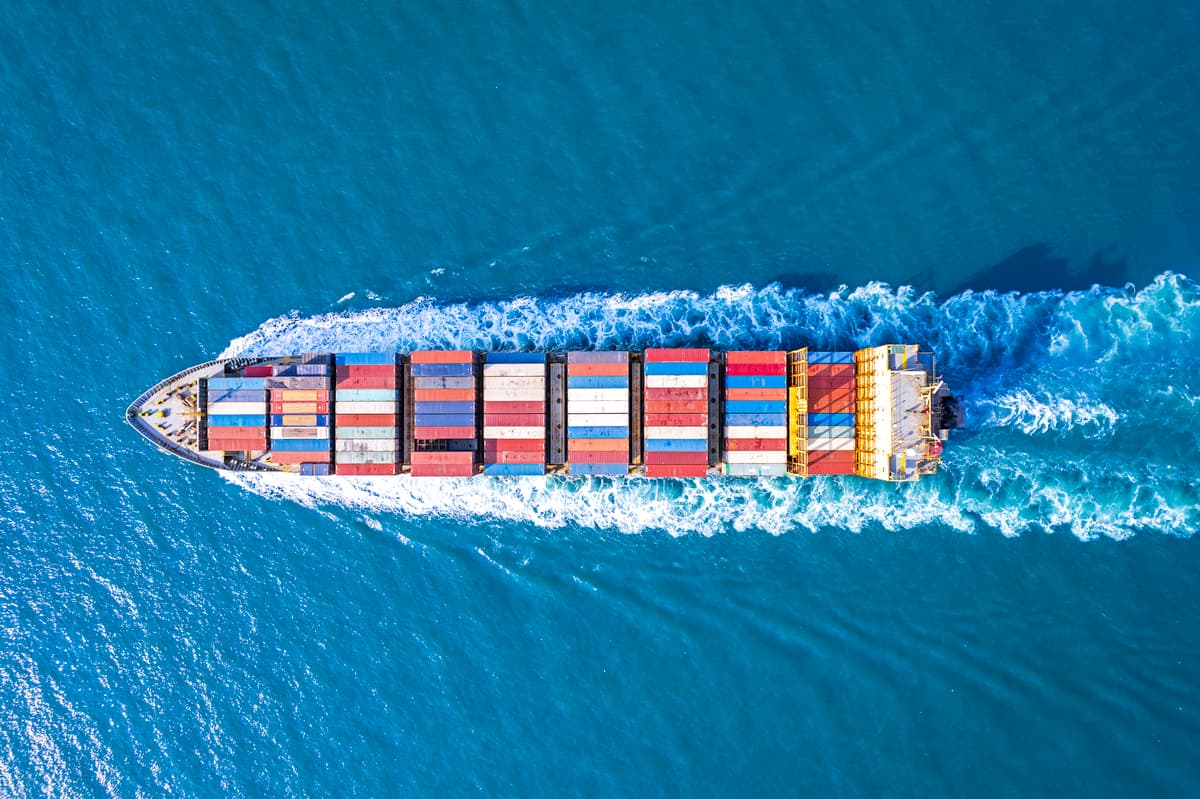
In this article
- Types of inventory
- The benefits of inventory management
- Key risks and challenges in supply chain inventory management
- Best practices for supply chain inventory management
- Modern technologies elevating inventory and supply chain management
- Integrating inventory management with other business processes
- What skills and qualifications are needed for inventory management?
Managing stock and logistics plays a central role in the success of any business, especially in the hospitality industry. For example, weekly inventory checks in food and beverage service can improve profits by up to 10% while reducing waste and helping simplify the task of re-ordering supplies.
In hospitality, inventory and supply chain management involves handling, getting, storing and distributing the goods needed for operating hotels, restaurants and other venues. This includes food, beverages, linens, toiletries and other items and means coordinating with suppliers to achieve timely delivery and quality standards. In this article, we’ll look at inventory and supply chain management in more depth, including some best practices, risks and challenges.
Types of inventory
Most businesses will stock goods, whether to be used in-house or for sale to customers. These items are known as inventory. There are plenty of different types of inventory, including:
- Raw materials: the basics used in manufacturing goods, these are in their unprocessed state and are converted into finished products through production processes, for example, raw cotton
- Work-in-Progress (WIP): consists of partially completed goods in various stages of the production process. These items are not yet finished but have undergone some level of processing, such as cotton that has been made into fabric
- Finished goods: products that have completed the production process and are ready for sale to customers. These are stocked in warehouses or retail outlets, for example, a cotton bedsheet
- Maintenance, repair and operations (MRO) inventory: items necessary for the upkeep of machinery and equipment used in production processes, such as oil
- Merchandise inventory: goods held by retailers for resale to customers, including items displayed on shelves or in storage areas awaiting purchase
What type of inventory do hospitality companies need to manage?
Hospitality venues such as hotels, restaurants and resorts must manage various types of inventory to ensure smooth operations and excellent guest experiences. Key categories include:
- Food and beverages: perishables such as fruits, vegetables, meats and beverages essential for dining services
- Housekeeping supplies: cleaning products, toiletries, paper products and cleaning equipment for maintaining cleanliness
- Linens and towels: bed sheets, pillowcases, blankets and towels to meet guest turnover and laundry needs
- Guest amenities: complimentary toiletries, bathrobes, slippers and in-room snacks to enhance guest experience
- Furniture and fixtures: beds, chairs, tables, lamps and decor items, requiring regular maintenance and replacements
- Operational supplies: office items, kitchen utensils and maintenance tools for daily operations
- Uniforms and staff apparel: appropriate apparel for staff to maintain a professional appearance and good hygiene standards
- Event and conference supplies: audio-visual equipment, tableware, seating arrangements and decorations for event hosting
- Emergency supplies: first aid kits, fire safety equipment and backup power sources for emergency preparedness
- Spa and wellness products: high-quality oils, lotions, skincare items and wellness equipment for spa services
The benefits of inventory management
Businesses must carefully manage goods and materials from ordering to storage and distribution. Supply chain inventory management makes sure the right amount of goods are available at the right time. This helps meet customer demand while minimizing costs and improving efficiency and cash flow. Some of the main benefits are:
- Operational efficiency: in hospitality, efficient inventory management is crucial for maintaining smooth operations. Hotels and restaurants rely on a consistent supply of food, beverages, linens and toiletries to avoid disruptions and ensure high-quality guest experiences
- Cash flow management: supply chain management helps control costs by securing cheap bulk rates while purchasing, reducing waste and avoiding overstocking. These savings can be reinvested into the business, boosting overall profitability
- Customer satisfaction and loyalty: good inventory management ensures popular menu items and essential amenities are always available, leading to positive reviews and repeat customers
- Supply chain resilience: having enough items in stock can help a hospitality business continue as normal even if supplies are disrupted
- Data-driven decision making: provides valuable insights into product performance, demand and market trends. This enables businesses to make informed decisions about products to order and pricing strategies
Key risks and challenges in supply chain inventory management
Managing inventory accurately can be complex. Among the main factors to consider are:
- Forecasting demand: fluctuations in market trends, consumer behavior and external factors such as economic conditions or natural disasters can make it challenging to predict sales accurately
- Inventory optimization: balancing stock levels to meet demand while minimizing excess stock requires real-time data analysis and complex software
- Supplier reliability: being reliant on vendors introduces risks of delays, quality issues or sudden disruptions in the supply chain
- Inventory shrinkage and loss: goods can go missing due to accidents, theft or oversight and this can cause discrepancies
- Transportation and logistics constraints: delays or disruptions in transport networks can interrupt the flow of goods and increase costs
- Technology integration: adding new technologies such as IoT sensors, RFID tracking or AI-driven analytics is important but has a significant cost
- Global supply chain risks: businesses can face geopolitical instability, trade disputes, currency fluctuations and regulatory complexities, all of which can cause issues in the supply chain
Best practices for supply chain inventory management
There are plenty of things that can help ensure effective inventory control and minimize risks and challenges in the supply chain. This is important in the hospitality industry to ensure guest satisfaction. The best practices to follow are:
- Demand forecasting accuracy: using advanced analytics and historical data to predict demand, considering market trends, seasonal variations and customer behavior
- Inventory optimization: working out the right amount of products to stock at any time. This helps businesses avoid running out of stock but also reduces shipping costs if having to frequently order more
- Supplier collaboration: building strong relationships with companies across the supply chain to improve reliability, streamline procurement processes and negotiate favorable terms
- Continuous monitoring and analysis: using real-time inventory tracking systems and analytics tools to check stock levels, identify trends and make data-driven decisions for replenishment and allocation
- Risk mitigation strategies: making contingency plans to address potential disruptions in the supply chain, such as shortages, delays or natural disasters
- Technology integration: applying solutions such as RFID, IoT sensors and cloud-based inventory management systems to automate processes and improve awareness of stock levels
You can learn about the right way to manage inventory in hospitality, along with many other aspects of hotel management, by studying a degree at a renowned school.
Develop business strategy skills, learn management theory and acquire real-world problem-solving abilities to excel in hospitality

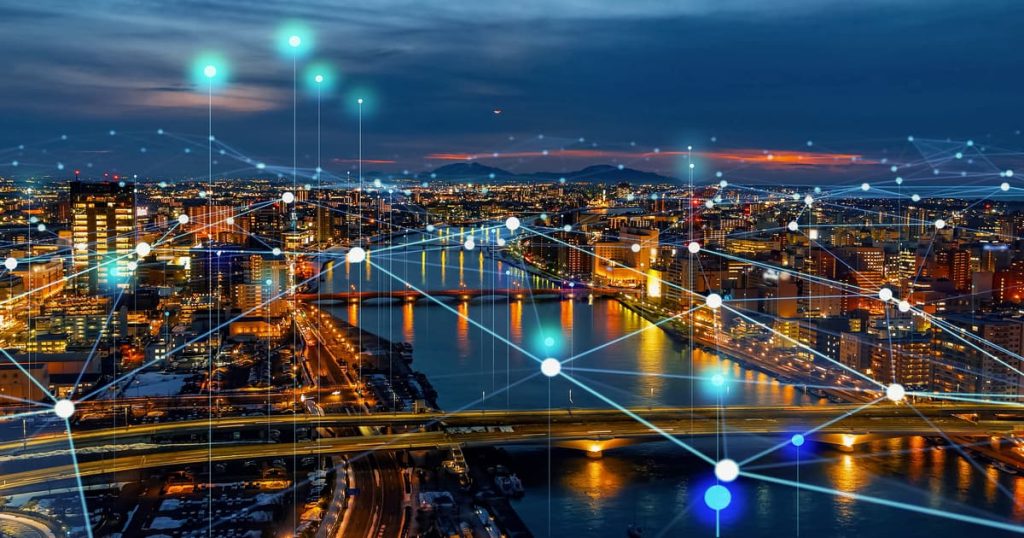
Modern technologies elevating inventory and supply chain management
Technology is revolutionizing how businesses manage their stock and logistics, improving efficiency, accuracy and responsiveness. Below, we’ll take a look at some of the key advances driving this transformation.
Internet of Things (IoT)
IoT dramatically changes supply chain management by using sensors and devices that constantly collect and transmit data. This connected system enables businesses to manage and monitor inventory in real time, improving logistics and ensuring stocks are refilled when needed.
Artificial Intelligence (AI) and Machine Learning (ML)
These tech solutions can identify patterns, trends and anomalies easily, which is important to help with decision making about inventory. AI is likely to predict demand for items much more accurately than humans can, which means supply managers can reduce excess inventory and improve replenishment times.
Robotics and automation
Automating repetitive tasks such as picking, packing and sorting can help to streamline the whole inventory process. This technology increases productivity, accuracy and speed, reduces labor costs and minimizes human error, leading to more efficient and reliable inventory management and supply chain processes.
Integrating inventory management with other business processes
Combining stock management and supply chain systems with broader operations can be a powerful way to improve efficiency. For example, hotels will need to integrate supply chain management with housekeeping services to get a clear idea of how many products are being used. This helps enable accurate demand forecasting, preventing stockouts or overstocking.
Businesses can do this by:
- Choosing compatible systems: using inventory management software or platforms capable of seamlessly integrating existing business processes
- Working with other departments: introducing inventory management solutions across key areas of the business, including procurement, sales and maintenance
- Standardizing procedures: establishing protocols that every department will follow
- Facilitating communication: providing open channels for real-time data sharing and collaboration between departments
What skills and qualifications are needed for inventory management?
Aspiring inventory managers need to develop a range of skills, including:
- Attention to detail: ensuring accuracy in inventory count and documentation to prevent discrepancies
- Organization: maintaining a well-structured system for tracking inventory and storage locations
- Analytical thinking: assessing data and trends to make informed decisions about inventory levels and procurement
- Time management: prioritizing tasks effectively to manage inventory efficiently and meet deadlines
- Communication: clearly conveying information to suppliers, team members and other stakeholders
- Problem-solving: identifying and resolving inventory-related issues quickly and effectively
- Negotiation: securing favorable terms and prices from suppliers to reduce costs
- Data entry: accurately inputting inventory information into management systems
- Financial acumen: understanding the financial implications of inventory decisions to manage costs
- Forecasting: predicting future inventory needs based on historical data and market trends
- Proficiency in inventory management software: using specialized tools to track and manage inventory efficiently
- Decision making: making timely and effective choices regarding inventory control and procurement
- Team collaboration: working effectively with other departments to coordinate inventory needs and usage
- Adaptability: adjusting strategies and processes in response to changing market conditions and demands
Hospitality schools such as Les Roches can help people acquire the essential skills and qualifications they need to become successful inventory managers. A hospitality degree often includes modules on procurement strategies, inventory management systems and supply chain logistics, which are reinforced by practical training and internships. By providing a blend of theoretical knowledge and hands-on experience, a hospitality education can help prepare students to handle the complexities of inventory and supply chain management.
Conclusion: the importance of mastering inventory management in modern supply chains
Managing stock efficiently is essential for operational success in today’s distribution networks. Efficient inventory management ensures the right products are available at the right time and place, preventing stockouts or excess inventory buildup. This directly impacts customer satisfaction, strengthening their trust and loyalty.
Effective inventory control also minimizes the costs of holding excess stock or rush orders. It allows for better resource allocation and cash flow management, improving overall financial health. In short, supply chain management is essential in business. Studying for a master’s degree in hospitality management can give you the tools you need to succeed in inventory management as well as in other key aspects of running a hospitality business.
Main Image: General_4530 / Moment via Getty Images